Mercedes-Benz Trucks, bu yılın Kasım ayı sonunda Wörth’teki Mercedes-Benz fabrikasında eActros 600‘ün seri üretiminin başlangıcını kutladı. eActros 600, yakın zamanda Hannover’deki IAA Transportation’da “2025 Yılının Uluslararası Kamyonu” seçildi. İlk eActros 600 müşteri araçları 2024 yılı sonundan önce üretilecek ve tescil edilecek. Her araca Gaggenau ve Kassel’deki Mercedes-Benz fabrikalarından gelen temel bileşenler takılacak.
Ana bileşenler Gaggenau’dan geliyor
Ağır ticari araçlar için şanzımanlarda uzmanlaşmış Gaggenau’daki Mercedes-Benz fabrikası şu anda elektrikli tahrik bileşenleri için bir uzmanlık merkezi haline geliyor. 2021’den beri dağıtım taşımacılığı için eActros 300/400 ve eEconic‘in e-aksı (aksı, motoru ve şanzımanı birleştiren ve elektrikli güç aktarma organını temsil eden bir ünite) için temel parçalar Gaggenau’da üretiliyor. Aynı durum, eActros 600‘e güç verecek yeni nesil elektrikli aksın merkezi bileşenleri için de geçerli olacak. Bunlar, Gaggenau’nun uzun yıllardır geleneksel tahrik hatlarına sahip araçlar için ürettiği türden mekanik parçalar. Bunlar, toplamda yaklaşık 30 farklı bileşen içeren son teknoloji ürünü, yenilikçi 4 vitesli aks tahriğini yapmak için kullanılıyor. Bunlara, şaftlar, dişliler ve senkromeç parçaları gibi özel olarak geliştirilmiş şanzıman bileşenleri ve kovan parçaları dahil. Gaggenau bu bileşenleri Kassel’e tedarik ediyor; burada aks ve şanzıman bileşenlerinin komple montajı gerçekleştiriliyor ve yeni geliştirilen, elektrikle çalışan arka aks yaratılıyor.
Ayrıca, eActros 600‘ün kabini için gövde parçaları da Gaggenau’da üretiliyor. Tedarik kapsamı, diğer şeylerin yanı sıra arka panel, tavan çerçevesi, bölme ve çapraz elemanlar gibi yapısal gövde parçaları ve çeşitli takviyeleri içeriyor. Bunlar, geleneksel olarak güçlendirilen kamyonlarda halihazırda kullanılan devralınmış parçalar. Tesisin gövde parçası uzmanlığı, böylece yeni akü elektrikli uzun yol kamyonunun yeni tasarlanmış kabininin dış derisini de üstleniyor.
Elektrikli güç aktarma organlarının tüm elemanları kalite, hizmet ömrü ve montaj alanı açısından sıkı gerekliliklere tabi. Örneğin, dişlilerin ve millerin dişlilerinin yüzeyleri ve pürüzlülüğü için geometrik özellikler yalnızca çok dar toleranslara izin veriyor. Özel dişli taşlama makineleri gibi en son ve son derece hassas üretim teknolojileri, gerekli kaliteyi garanti etmeyi mümkün kılıyor.
Kovan parçalarının mekanik işlenmesi Gaggenau fabrikasında özel olarak dönüştürülmüş bir salonda gerçekleşiyor. Burada otomatik işleme merkezlerine sahip tamamen yeni bir üretim tesisi kuruldu. Tedarik aşamasında, bu merkezlerin sanal olarak devreye alınması, işlemenin “dijital ikizler” üzerinde simüle edilmesini sağladı. Bu süreç, geleneksel bir üretim tesisi kurulum sürecine kıyasla muazzam bir zaman tasarrufu sağlıyor. Mekanik işleme, kovanlar sızdırmazlık testinden geçmeden önce delme ve frezeleme ile diş açma işlemlerini içeriyor.
Mercedes-Benz Gaggenau Fabrikası Fabrika Müdürü Thomas Twork, konuyla ilgili olarak “Geçmiş olmadan gelecek olmaz. Gaggenau’daki Mercedes-Benz fabrikasında gelenek ve dönüşüm el ele gider. Yüksek hassasiyetli şanzıman bileşenlerinin üretimindeki onlarca yıllık deneyimimizi yeni elektrikli güç aktarma organına uygulamaktan gurur duyuyoruz. Kassel’deki montaj fabrikasındaki meslektaşlarımızla birlikte fabrikamız yayımsız mobiliteye önemli bir katkı sağlıyor.” dedi.
Daimler Truck Grup İş Konseyi Başkanı ve Mercedes-Benz Gaggenau Fabrikası İş Konseyi Başkanı Michael Brecht ise şunları söyledi: “Özellikle e-aks için üretim hacimleri, Kassel tesisiyle bir üretim ağı anlamına geliyor. Birlikte, yeni elektrikli güç aktarma organına önemli bir katkı sağlıyoruz. Bu şekilde yenilikler üretiyoruz ve ayrıca iş gücüne yeni teknoloji konularını ele alabilmemiz için oryantasyon sağlıyoruz.”
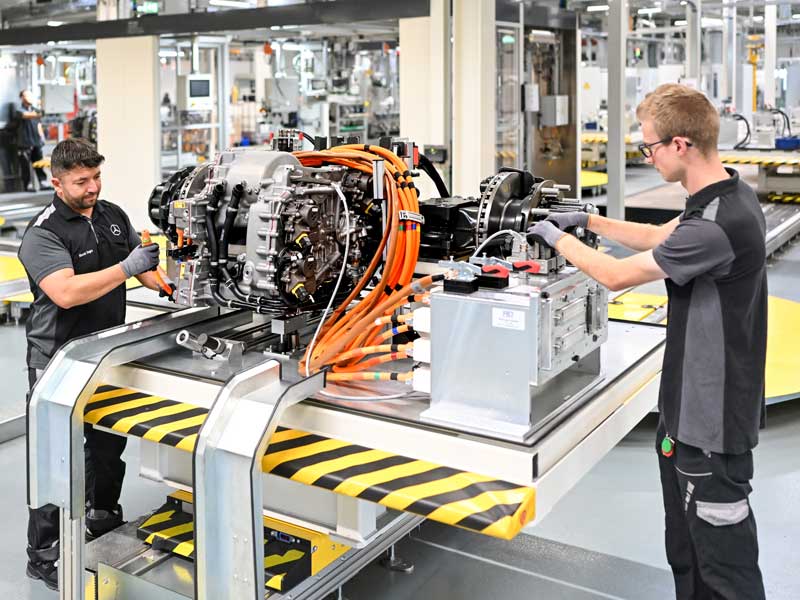
Yeni geliştirilen e-aks Kassel’de geliştiriliyor
Geleneksel akslar ve elektrikli tahrik sistemleri için küresel mükemmellik merkezi olan Kassel’deki Mercedes-Benz fabrikası, eActros 600 için yeni nesil e-aksı birleştiriyor. Elektrikle çalışan arka aks, özellikle uzun mesafe taşımacılığı için yeniden tasarlandı. Daha yüksek performans ve verimlilik için bir dizi teknik yenilik sunuyor.
Bu amaçla tesiste, işlevsel ve güvenlikle ilgili özellikler için test ve muayene istasyonları da dahil olmak üzere yeni bir montaj hattı inşa edildi. Şu anda eActros 300/400 ve eEconic‘te kullanılan ve halihazırda Kassel’de üretilen e-aks için olduğu gibi, yeni nesil için de “ortak parça ilkesi” geçerli. Bu, aks kovanının yanı sıra tekerlek ucu ve fren bileşenlerinin, Kassel tesisinin yirmi yıldan uzun süredir ürettiği geleneksel akstan geldiği anlamına geliyor. Bileşenler montaj hattında oldukça esnek bir şekilde üretiliyor, böylece tesis sipariş durumuna bağlı olarak geleneksel ve elektrikli akslar arasında değişiklik yapabiliyor.
Yeni nesil E-aks, aks kemeri ve elektrik motorları ile şanzıman ve yüksek gerilim bileşenlerinden oluşan elektrikli tahrik sisteminden oluşuyor.
Kassel’de yeni nesil E-aksın montaj süreci
Kassel tesisindeki bütüncül montaj süreci çeşitli koordineli aşamalarda gerçekleşiyor. Aks taşıyıcısı yeni e-aksın temelini oluşturuyor ve ilk adımda süspansiyon, yuvarlanma ve frenleme için hazırlanıyor – yani tekerlek poryaları, tahrik milleri ve fren kampanaları buraya monte ediliyor. E-aksın aks taşıyıcısı geleneksel seriyle aynı, bu nedenle mevcut araç şasisine kolayca uyarlanabiliyor.
Elektrikli tahrik ünitesinin montaj alanında, önceden monte edilmiş şanzıman parçaları, iki elektrik motoru ve diğer bileşenler Gaggenau’dan gelen aks taşıyıcı kovanına yerleştiriliyor. Son montajda, daha önce oluşturulan elektrikli tahrik ünitesi ile aks köprüsü arasındaki evlilik gerçekleşiyor. Ayrıca, çeşitli sensörler, yağ ve soğutma hatları ve düşük voltajlı kablo setleri elektrik olmadan monte ediliyor.
Elektrikli aks, Kassel’deki Mercedes-Benz tesisinden ayrılmadan önce, son aşamada mekanik ve elektrikli bileşenler ayrıntılı bir işlevsel testten, yani “hat sonu testi“nden (EOL testi) geçiyor. Burada yüksek gerilim kabloları takılıyor, kaçak testi yapılıyor ve yüksek gerilim testleri gerçekleştiriliyor. Son olarak elektrikli aks; yük, topografya ve vites seçimi profilleri dahil olmak üzere çeşitli sürüş durumlarının simülasyonuna tabi tutuluyor. EOL testini geçtikten sonra e-aks, Wörth’teki Mercedes-Benz tesisine nakliye için hazırlanıyor.
Mercedes-Benz Kassel Fabrikası Fabrika Müdürü Hauke Schuler de şu açıklamayı yaptı: “Ürün portföyümüzde artık CO2 nötr uzun mesafe taşımacılığı için bir e-aksımız da olduğu için gururluyuz. Elektrikli tahriği mevcut aks kavramına entegre eden benzersiz ve verimli tasarımıyla eActros 600’ün uzun menziline katkıda bulunuyor. Bu, Kassel’deki Mercedes-Benz fabrikasının yayımsız mobiliteye dönüşümünde bir diğer önemli kilometre taşı.”
Daimler Truck Genel İş Konseyi Başkan Yardımcısı ve Mercedes-Benz Kassel İş Konseyi Başkanı Jörg Lorz ise şu değerlendirmeyi yaptı: “Mercedes-Benz Kassel fabrikasındaki ekibimiz yeni E-aksın üretimi konusunda tutkulu. Bu sayede Daimler Truck’taki bu yenilikçi yeni tahrik teknolojisinin başarısına önemli bir katkıda bulunuyoruz. Gaggenau fabrikasıyla birlikte ortak üretim ve teknoloji ağını temsil ediyor.”