SAF-HOLLAND will deliver its SAF INTRA axles with the optional zinc-free SAF PREMIUM COATED powder coating. It protects the axles against corrosion damage caused by weather and dirt and gives the vehicles a neat appearance over many years. This gives trucks, tanker trucks and silo vehicles a longer service life and a higher resale value and consequently makes them more economical.
Complex operating conditions – such as road salt in winter or dirt at landfill and construction sites – can promote corrosion on the SAF INTRA axles. SAF PREMIUM COATED, a multi-stage coating process with powder coating, reliably prevents corrosion. “We are currently the only axle manufacturer that offers an additional zinc-free coating in the 9-ton segment,” says Alexandre Charpiot, Vice President Sales OEM.
Higher resale value from additional coating
The improved corrosion protection extends the service life of the axles and ensures a neat appearance of the vehicle fleet. This allows owners to count on a higher resale value, in particular in the case of high-quality tanker and silo bodies. Fleet operators also benefit from the high coverage and the optimum mechanical properties of the powder coating. In addition, the coated axles are resistant to impact, light, chemicals and extreme temperatures. SAF-HOLLAND offers a ten-year anticorrosion warranty against corrosion on its SAF PREMIUM COATED axles.
The coating is applied to the axle beam and also to the steering arm for steering axles. Other add-on parts such as brakes or wheel ends are not coated. The benefit of the SAF PREMIUM COATED axles for vehicle manufacturers: The coated axles can be painted over if necessary and can be sold at a surcharge directly ex factory in the case of expensive bodies such as silo vehicles or tankers. What is more – the installation of the corrosion-protected axles is identical to installing standard SAF-HOLLAND products.
All-round protection and high-quality appearance
The four-layer SAF PREMIUM COATED process optimises the technical properties of the rigid and steered SAF INTRA axles: In the first step, airless blast cleaning prepares the surface of the welded axle beam, breaks sharp edges and removes silicates from the welding process. Then a standard cathodic dip coating is applied to the axle as a basis for the next coats.
In the third stage, the axle is primed with a zinc-free epoxy-resin powder that offers good adhesion and protects against corrosion. The final powder coating on polyester resin basis in colour DB703 Iron Mica Metallic has optimum mechanical properties and gives the axle a high-quality appearance.
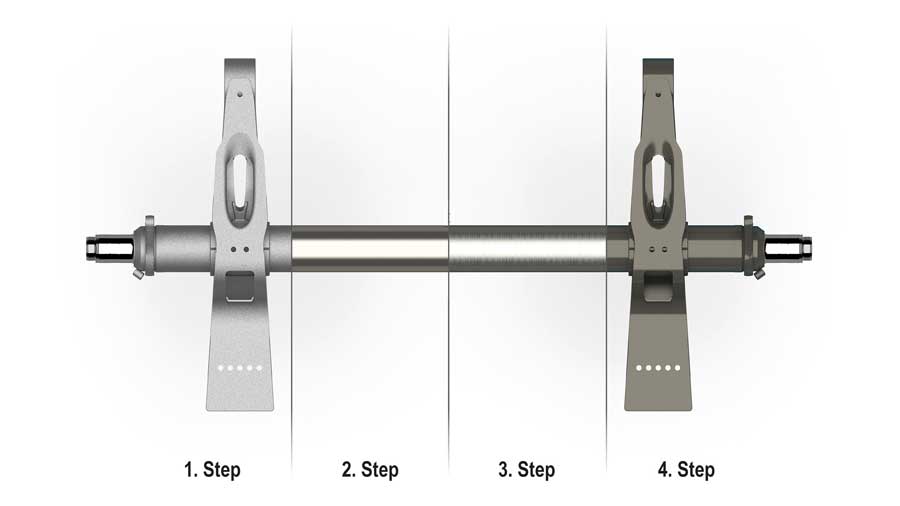
Environmentally friendly, high-performance additional coating
“Together with the top coat powder, the zinc-free corrosion protection powder forms a perfectly coordinated protection system. With the same performance level, it is significantly more environmentally friendly than zinc solutions containing hazardous substances,” explains Alexandre Charpiot. The additional coating of the SAF INTRA axles also has a positive impact on the test results, as the manufacturer indicates: In the salt spray test as per DIN EN ISO 9227, there was no visible corrosion on the surfaces or edges even after four times the test duration of 2,000 hours.
SAF PREMIUM COATED for standard and offroad applications
The SAF PREMIUM COATED process is suitable for a number of models from the SAF INTRA series with different suspension arm versions, as well as for standard and offroad applications: for all axle types of the rigid SAF INTRADRUM axles and for the rigid SAF INTRADISC axles with the exception of the electric axles and the hydraulically driven SAF INTRA CD TRAK axles. For steered axles, the special coating can also be applied to almost all variants with disc brakes.