Autonomous driving, electric vehicles, new business models and a highly skilled workforce: with the ‘GRIP 2030’ strategy, Volkswagen Commercial Vehicles (VWCV) is continuing to push on with the transformation of the brand into a leading supplier for sustainable mobility solutions. Today, Herbert Diess, Chair of the Board of Management of Volkswagen AG, Thomas Schäfer, CEO of the Volkswagen Brand and of the Brand Group Volume, along with other Group management board members and Daniela Cavallo, Chair of the Full and Group Works Council, met at the VWCV main plant in Hannover to discuss the brand’s strategic objectives and the site’s future focus.
“The Hannover plant’s transformation is symbolic of the brand’s far-reaching change”, said Carsten Intra, Chair of the VWCV Brand Management Board. “In line with our ‘GRIP 2030’ strategy, we will increase the electric proportion of our fleet to more than 55 per cent by the end of the decade. We’ve laid the foundations for that this year with the start of production of the ID. Buzz. We are further gearing up the production operation to the manufacture of electric vehicles and are training up the workforce for the future tasks in a highly automated, digital factory.”
The technological change at the site had been particularly noticeable over the last three years, said Intra. “We now have some areas in the factory where 93 per cent of the tasks are done by robots.” Successfully transforming the workforce at the same time was one of the strategic pillars in this process, he said. “A modern factory calls for the employees to have new skills too. Taking them with us into the future is one of the brand’s most important tasks. Along with the works council, we’ve made the right decisions for doing this and will be investing 21 million euros between now and the end of the decade in upskilling”, emphasises Intra.
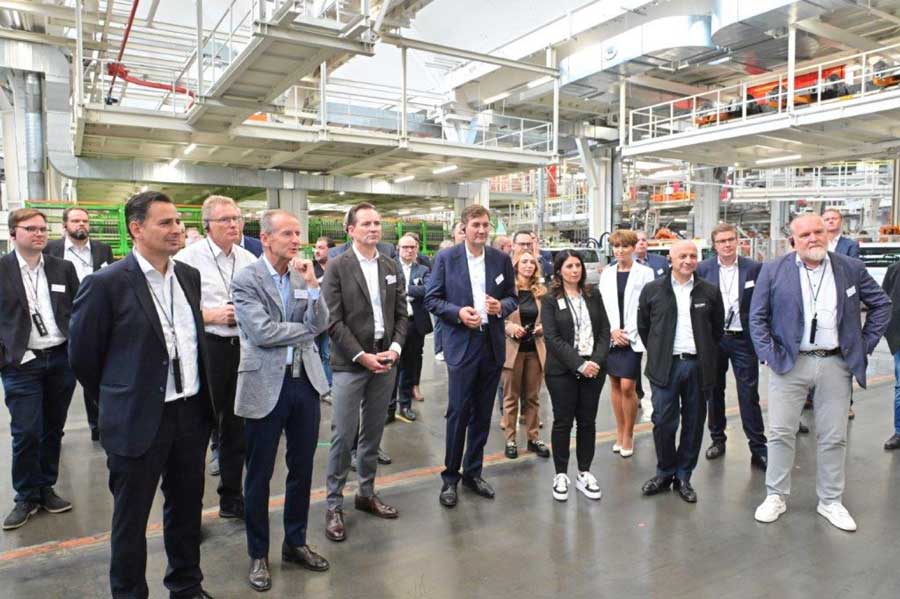
“Volkswagen Commercial Vehicles is systematically focussing itself on the future”, was a point also stressed by Thomas Schäfer, CEO of the Volkswagen Passenger Cars Brand, Member of the Volkswagen AG Board of Management and Head of the Brand Group Volume. “With the electrification of the portfolio and with the Centre of Excellence for Autonomous Driving, the team led by Carsten Intra are addressing the right issues. The ID. Buzz is a brand-shaper for Volkswagen and is generating enthusiastic reactions all over the world. With the successful start of production in Hannover, the workforce has demonstrated its capabilities. With over 10,000 advance sales, the order books are well-filled, and production is now being ramped up further. The ID. Buzz is a good example of what we can achieve in the High-Volume Brand Group when we work together as partners and utilise the synergies.”
Full and Group Works Council Chair Daniela Cavallo said: “Hannover is a proud site with a great tradition – and excellent prospects. The plant has in the past already repeatedly proved its ability to change – thanks to its flexible and highly skilled workforce. And its precisely in that, namely in the skills and knowledge of our colleagues, that we’re now also systematically investing further. For it is precisely this know-how, alongside convincing products, that is the key to success. Our good experiences from the upskilling programmes in Zwickau and Emden are helping in this process. I’m therefore convinced: VWCV in Hannover will in future continue to be a shining example in our industry of tradition with a future.”
During the Site Symposium, staff from the production department gave a presentation of modern technologies in the production facility. For example, Hendrik Volksmann, a machine operator in the body shop, demonstrated the practical use of a smart watch. Volksmann gets important information about the plant and machinery sent directly to his wrist, and is thus able to promptly identify and remedy any issues, for instance with the robots.
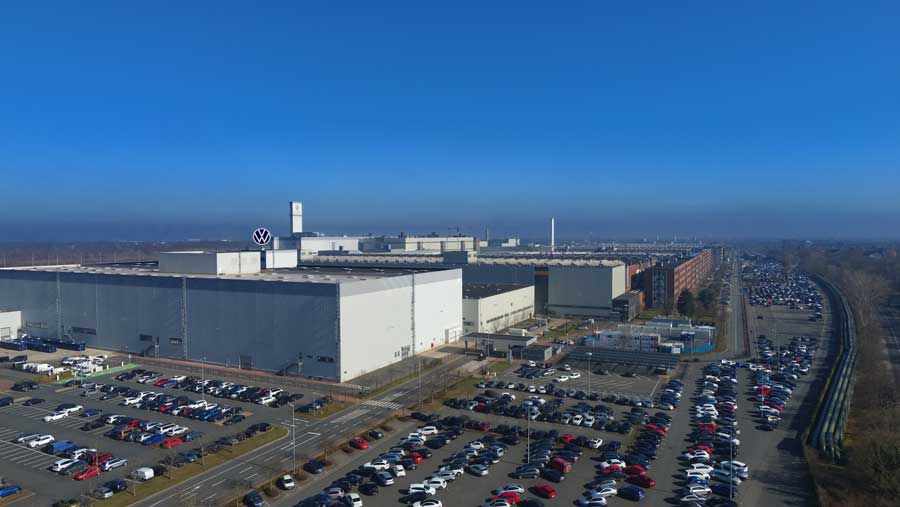
Particular focus was placed on the changes since the last symposium at the site in 2019, prior to the coronavirus pandemic, and the successful start-ups of the new Multivan and ID. Buzz.
These included:
Production:
- Increased efficiency as a result of an automatic stacking system in the press shop: after being pressed, parts get automatically piled up into stacks by robots.
- Commissioning of a new plate-cutting system in the press shop, replacing multiple old systems. The system cuts the supplied steel coils into the respective pieces of plate required for further working in the press shop.
- Digitalisation and automation in the body shop: in the new bodyshop buildings there is no longer any need for synchronised, repetitive insertion of parts. Robots now take the parts straight out of containers.
- Modernised assembly facility with new line sections for electrical features and with improved ergonomics.
Personnel:
- For the training of the workforce in skills of the future, Volkswagen Commercial Vehicles is investing a total of 21 million euros between now and the end of the decade.
- Around 29,000 training days in total for vehicle start-ups: 5,000 employees were intensively upskilled on the start-ups of the new Multivan and ID. Buzz.
- Start of transformation programmes in which employees are trained on tasks that will be increasingly needed in the future in the production operation. Example: production workers gaining the skills in 180 days to become data analysts.
Infrastructure and logistics:
- Construction of a new logistics centre (16,000 square metres) and a bridge linking it to the production facility.
- Commissioning of an XXL lift (23 metres long and 3 metres wide) for self-driving transporter trains up to 20 metres long and able to carry up to 45 tonnes.
- Start of construction of a new production hall for future vehicle production.
- Expansion of the autonomously performed transport tasks in the production operation: around 40 per cent of the transportation of parts in the vehicle production process is being done by self-driving transport vehicles.