Following the success of a trial loading operation performed in Denmark in mid-July, the DOLL wind blade transport system has been certified by Vestas. The system’s list of approvals now extends to every major turbine manufacturer.
The certification by Vestas, one of the world’s biggest wind turbine manufacturer, marks yet another milestone for the DOLL wind blade transport system. “Our system has now received approval from every major turbine manufacturer”, says Rolf Gerhardt, Senior Product Manager at DOLL Fahrzeugbau GmbH. “This will make it much easier for our customers to plan their projects, even if they are working with a range of different clients and tendering processes.”
The concept behind DOLL’s wind blade transport system involves mechanical or hydraulic lifting adapters with replaceable mounts for the root frame, a self-steering trailer with hydraulic steering and DOLL vario axle technology, plus special bolsters for accommodating the wing tips. The lifting adapters are mounted on the traction unit or an additional dolly, depending on the weight of the wind blade, and the swap bodies for the special bolsters can be adapted to various TIP frames.
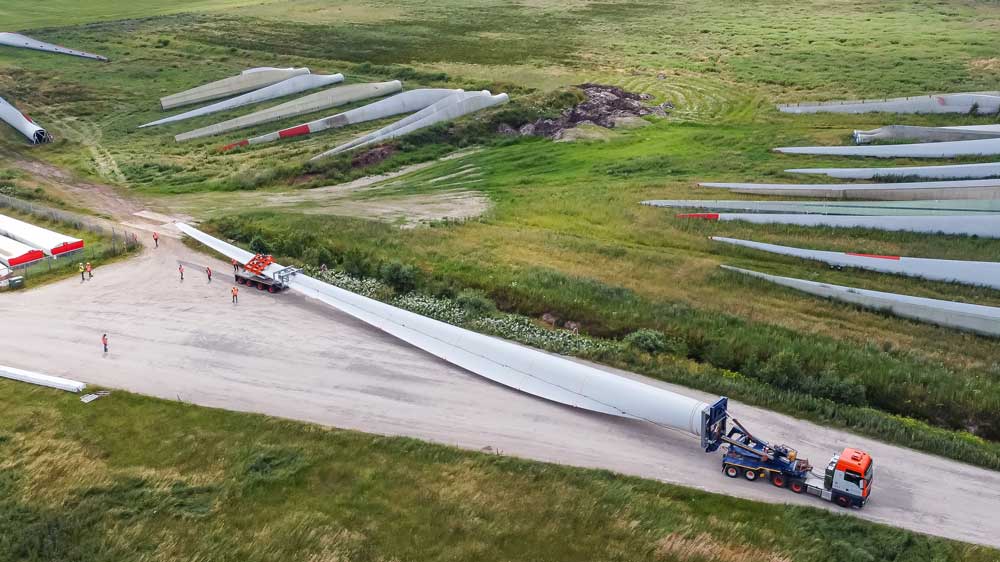
Fine-tuned and proven in practice
“One of the biggest jobs in this case was designing a pendulum frame for accommodating a Vestas hydraulic friction clamp. The frame compensates for the forces and torsional moments that the wing tip is exposed to during transport”, explains Rolf Gerhardt. The other adapter parts, used for a range of mechanical, hydraulic and electronic interfaces, can be assembled in the self-steering trailer combination with speed, ease and reliability. The entire structure was fine-tuned with a large amount of input from Vestas and with practical support from Universal Transport during a trial loading operation in Denmark – leading to Vestas approving the transport system with immediate effect.
In practice, a single DOLL transport system is able to accommodate wind blades from every major manufacturer – all it needs are the attachment parts and adapters specific to the manufacturer in question. DOLL’s self-steering trailer system is approved for transporting specifically the following blades and rotor blades:
Enercon: E138, E147 (LM71.8), E160 (LM78.3)
General Electric: WT19 (LM77.4)
Nordex: NR65.5, NR74.5, NR77.5, NR81.5
Siemens Gamesa: SG155, SG170
Vestas: EnVentus V150, EnVentus V162
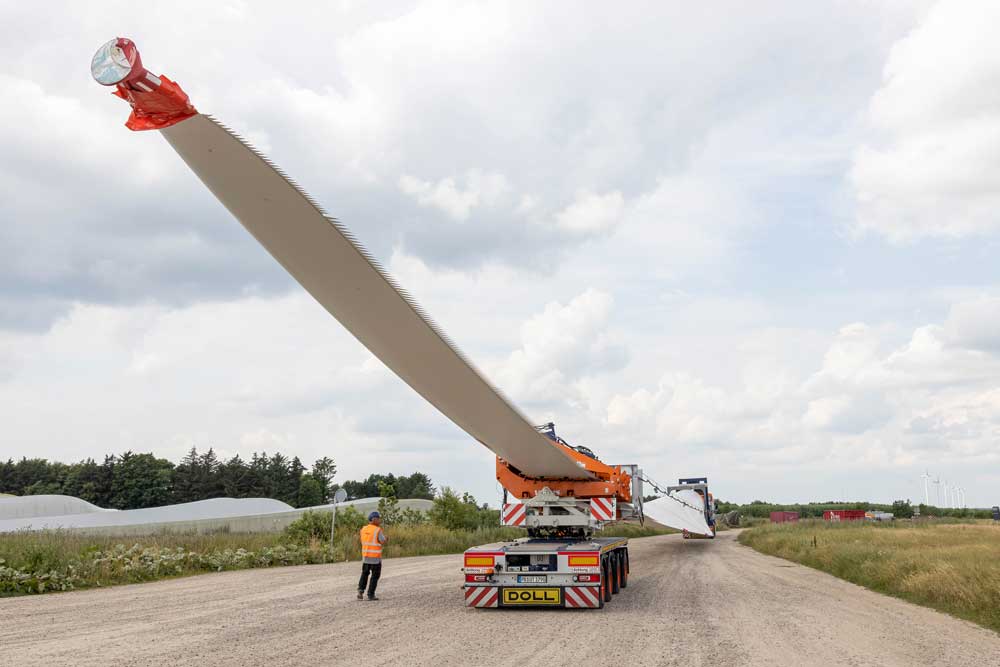
Decades of experience
DOLL’s wind blade transport system is the product of the company’s decades of experience in self-steering trailer technology – designed for round timber and long items of various kinds. The special combinations it has developed for the wind energy industry are suitable for rotor blades of up to 35 tons in weight and 100 metres in length. The lifting adapters for accommodating root frames are dimensioned for fifth-wheel loads of up to 32 tons, with a combined pivot/rocker bearing system ensuring that the rotor blade and rocker bearing rock uniformly over the pivot point on the traction unit. As a result, no torsional moments arise and transportation remains safe, even when the load has a high centre of gravity.
Other features of the self-steering trailer combinations are short loading times, reliable operation and excellent manoeuvring characteristics. Thanks to the extensive clearance between the towing vehicle and self-steering trailer (without low telescopic beams of the kind found on semi low-loaders), crossing over crash barriers and other obstacles is a breeze. Not only that, but the hydraulic suspension on the self-steering trailer and the large slewing ring steering angle (with a bolster impact of up to 85 degrees on the left and right) enable a manoeuvring range that extends to lateral movement.
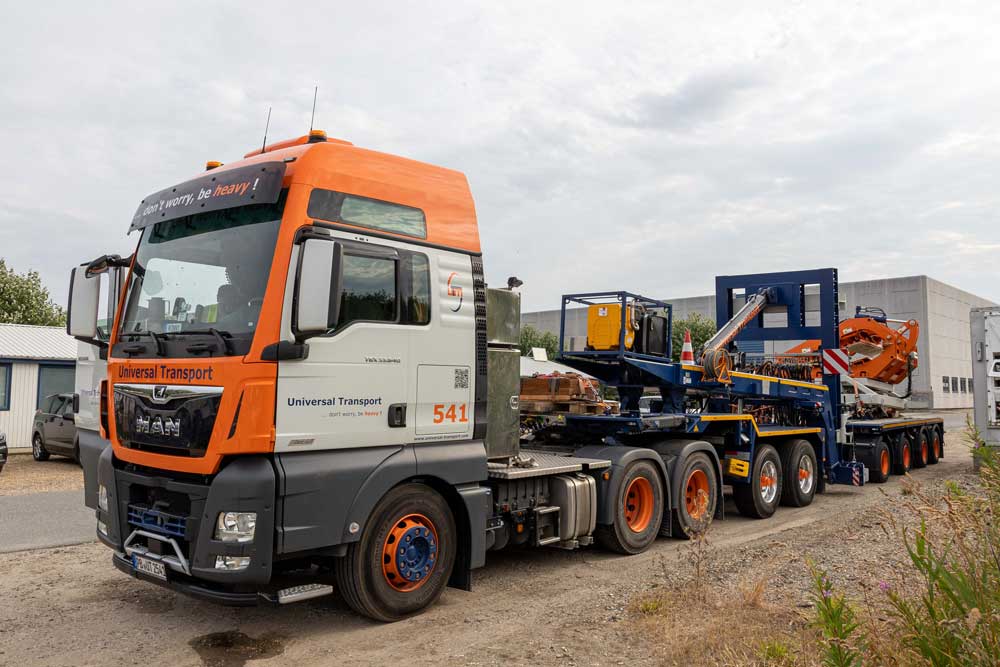
Equipped for the future
DOLL worked with leading wind turbine manufacturers from the very start when developing its transport system. The adaptations, which are tailored to each type of rotor blade, were coordinated jointly with the manufacturers and then subjected to practical tests. The first successful test drives – involving the Nordex NR74.5 – were conducted back in mid-2019. DOLL is set to continue with its tried-and-tested method, which it also conducted with Vestas, as it moves into the future – but it doesn’t intend to keep things static. As the future brings wind blade designs with changes in length, girth, shape, weight and centre of gravity, it will present new challenges to which DOLL will need to respond with appropriate adaptation options.